Advanced Manufacturing Processes and Systems
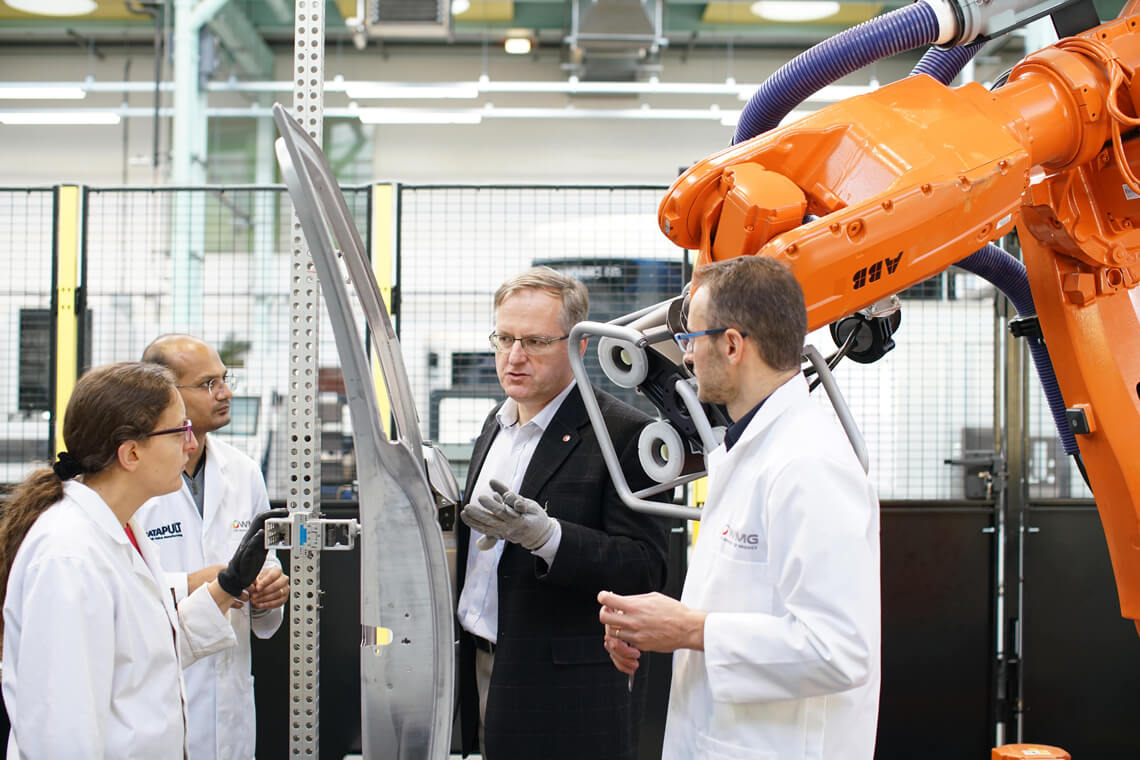
Advanced Manufacturing Processes and Systems (AMPS)
Getting data right first time
Our research focuses on integrating products, processes, and complex services to create closed-loop systems with capabilities to self-recover from product failures and changes.
We work across digital design and manufacturing, process monitoring and control, and industrial systems with one ultimate goal – to achieve a ‘right-first-time’ capability.
The principles that guide closed-loop production systems and factories are underpinned by the fact that manufacturing processes, products, and interlinked services are challenged by rapidly evolving external drivers including new materials, new regulations, new technologies, and sustainability, along with services and communications systems in an intensely cost-pressured environment. Meeting these challenges demands the development of new enabling technologies
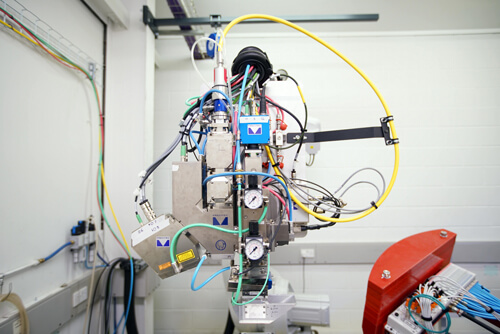
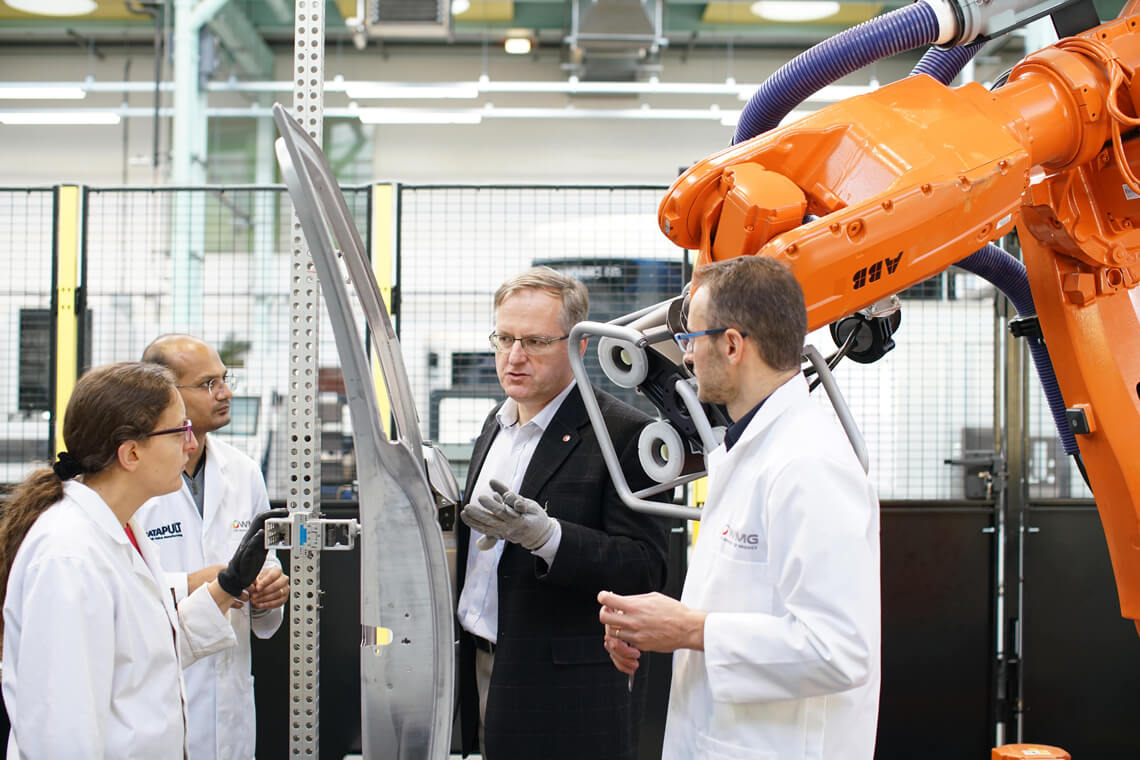
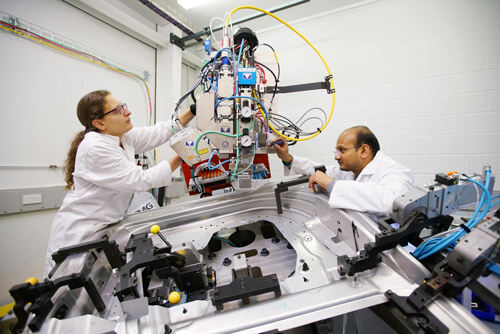
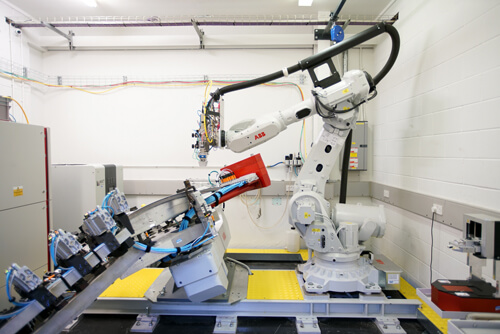
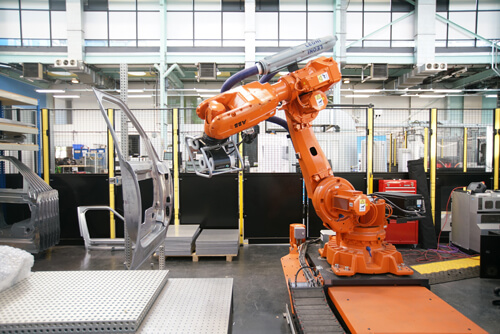
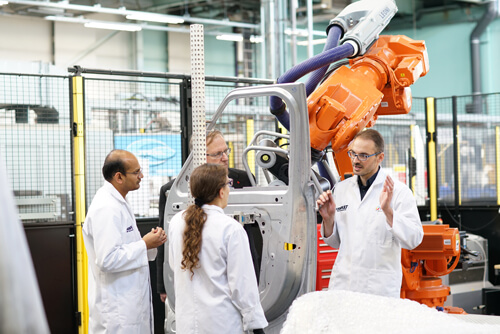
Research Tracks
We have four major research tracks:
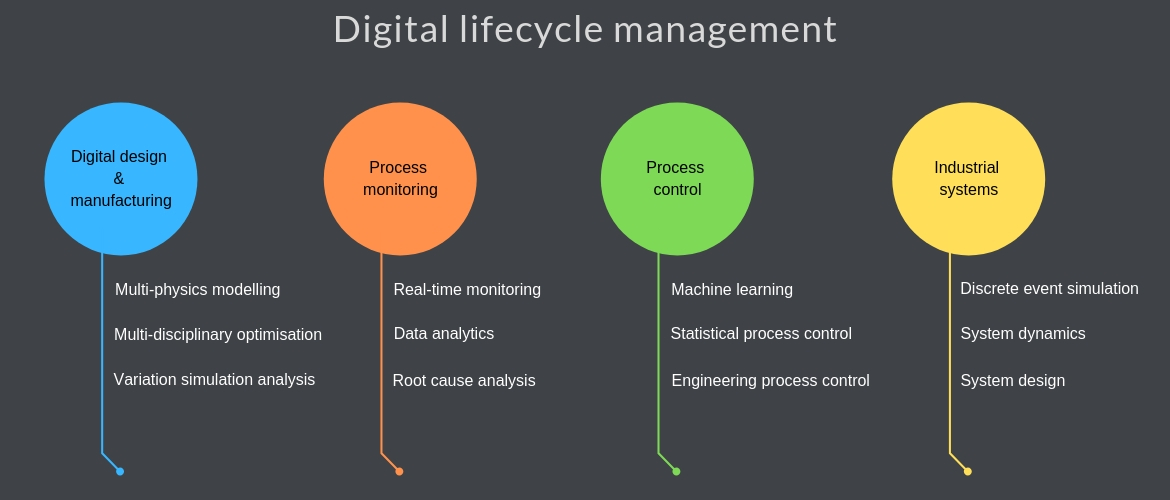
Focus areas
Digital Design & Manufacturing
We aim to develop simulation tools for predicting assembly system behavior early in the design stage, with a focus on achieving a "right-first-time" capability. Addressing challenges like statistical variation modeling and geometric variations, the approach integrates stochastic models with PLM tools, develops mechanisms for multi-stage assembly variations, and employs a design synthesis strategy. The ultimate goal is to minimize defects at both single-stage and multi-stage levels through stochastic robust optimisation.Process Monitoring
We aim to achieve zero-defect manufacturing through closed-loop quality control, focusing on rapid and intelligent defect monitoring and diagnostics. Traditional defect diagnostic approaches are overcome by employing multivariate statistical process control (M-SPC) analysis. However, challenges persist due to complex non-linear relationships, coupled models, and a high-dimensional parameter space in multi-stage assembly systems. The approach treats each manufacturing process stage as a stochastic event, representing the functional relationship as a stochastic multivariate function for real-time defect identification with adaptive measurement strategies.Industrial System - Application for Healthcare System
We seek to develop systematic methodologies and simulation tools integrating care processes, resources, and complex service system information to reduce and prevent unnecessary variation in patient care, enhancing overall quality improvement. Challenges include accurately modeling the patient journey, understanding the propagation of unnecessary variation, and addressing the complex relationship between care-related processes and quality indicators. The approach involves integrating process-related measurements with key performance indicator data to comprehend, reduce, and prevent variations in patient care throughout the service system.Process Control
We aim for zero-defect manufacturing with closed-loop quality control, focusing on in-process rapid adjustment and control architecture. Challenges in current data-driven approaches, like partial open-loop control and prediction accuracy issues, drive a proposed shift to model-based methods. This includes self-optimizing systems for corrective and preventive actions based on model-based reasoning. Challenges include handling diverse spatial and temporal data, optimizing real-time fault diagnosis, and integrating in-process data feedback into product/process design. The vision is to address defects causing quality deterioration using advanced algorithms for multi-physics defect simulation, intelligent root cause analysis, and a sophisticated knowledge repository with machine learning models.Insights
Uni-WARP project supports companies in a shift to transport electrification
Transport is now the highest emitting sector of the UK economy, accounting for 22% of total green-house gas emissions. The Government has announced plans to make every mode of transport net zero emissions by 2050 and has set ambitious decarbonisation targets. Electric vehicles (EVs) are seeing a surge in demand, with sales of battery electric and plug-in hybrid vehicles accounting for over 13% of sales in January 2021 compared with 6% in 2020 (Society of Motor Manufacturers and Traders, SMMT). But market opportunities in other transport sectors, such as two-wheeled vehicles, aerospace and marine, are growing significantly.
Digital
Manufacturers leave seat manufacturer sitting pretty
Car manufacturing in the UK is changing radically, as the electrification is forcing innovation and design change of almost all parts of cars. Industry leaders are challenged to change design radically, launch new products more quickly, while maintaining quality levels and costs. To keep up with this, many manufacturers in the supply chain are already embracing digital technologies to connect their factories, improve processes and reduce costs. By embracing digitalisation, the electrification of the automotive sector could unlock growth of up to £75bn by 2035, benefitting the entire supply chain.