Steels - Casting innovation in steel research
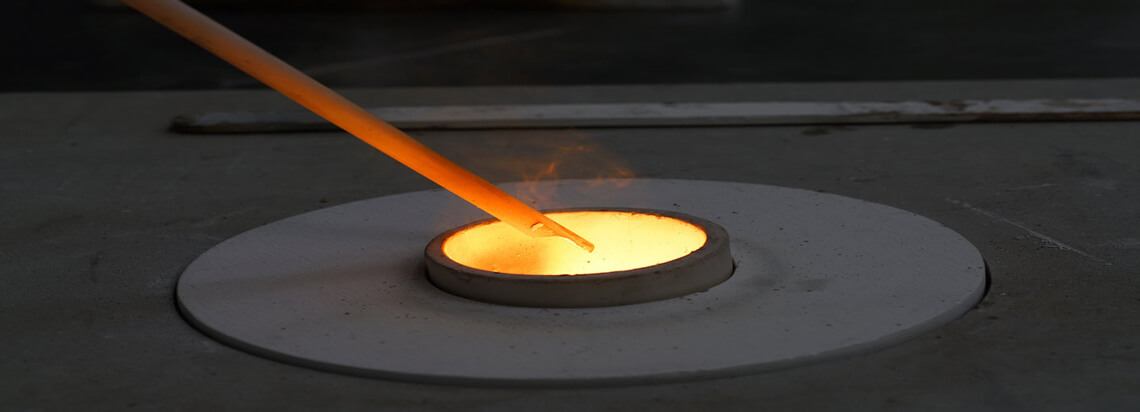
Advanced Steel Research Centre
Casting innovation in steel research
Conducting both fundamental and applied research, we enhance steel processing, develop advanced materials, and focus on improving steel performance.
Our team explores physical-chemical aspects throughout iron and steel manufacturing, covering processes such as steelmaking, casting, forming, coating, and joining. Rapid alloy processing facilities expedite new development.
The Advanced Steel Research Centre (ASRC) works to support the steel industry, our research ranges from fundamental metallurgy for new steels, to steel applications and support for policymakers. We are one of the largest steel research group in the UK with expertise in steelmaking production techniques including casting, forming, coating, joining, product performance, inspection, characterisation and measurement.
Research capabilities in the ASRC include rapid alloy processing, ironmaking, casting simulation for steel prototyping, thermo-mechanical processing, and high temperature experimentation.
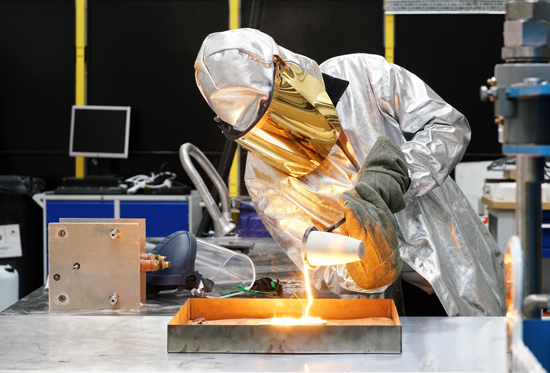
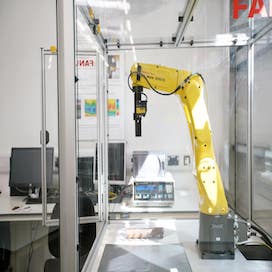

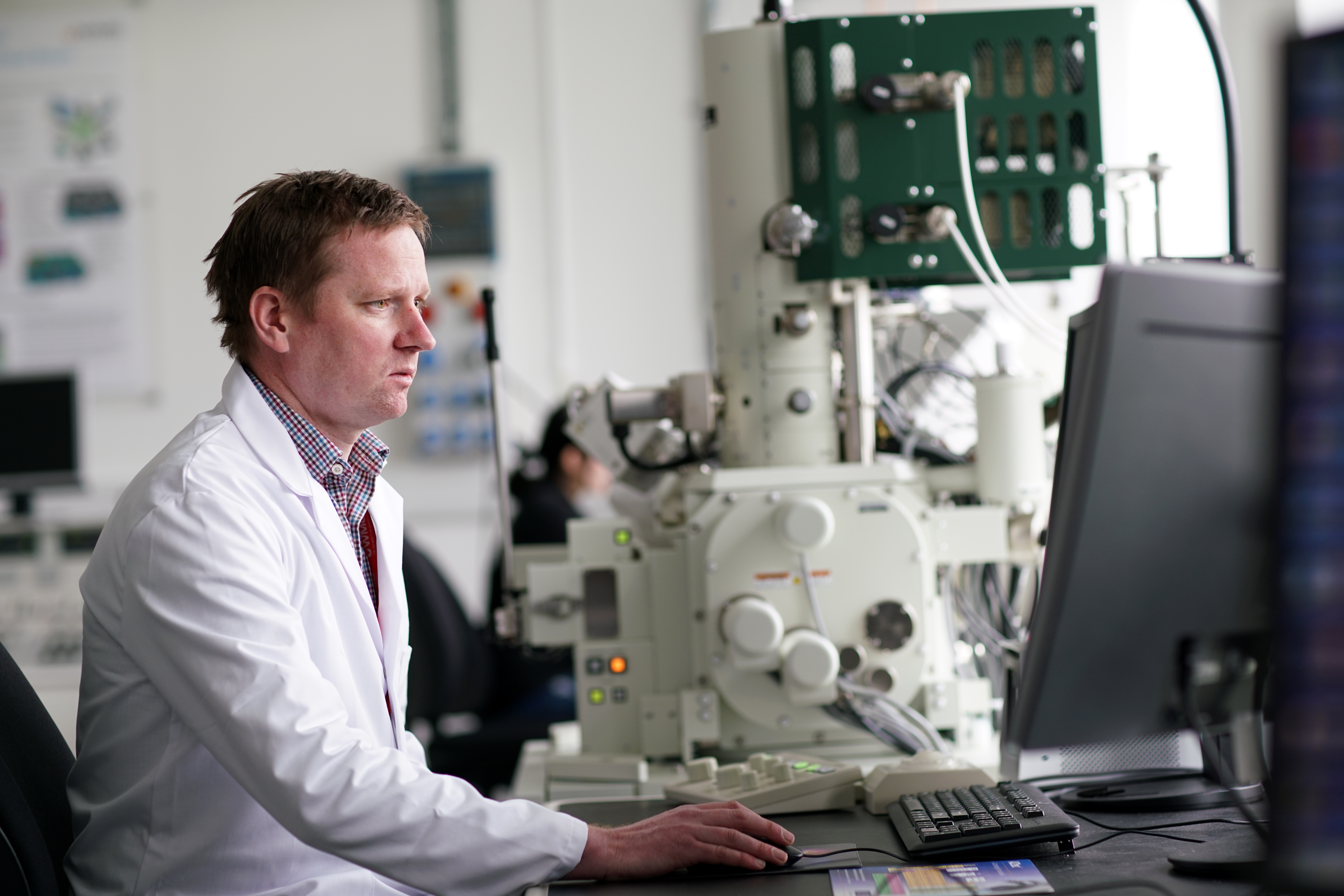
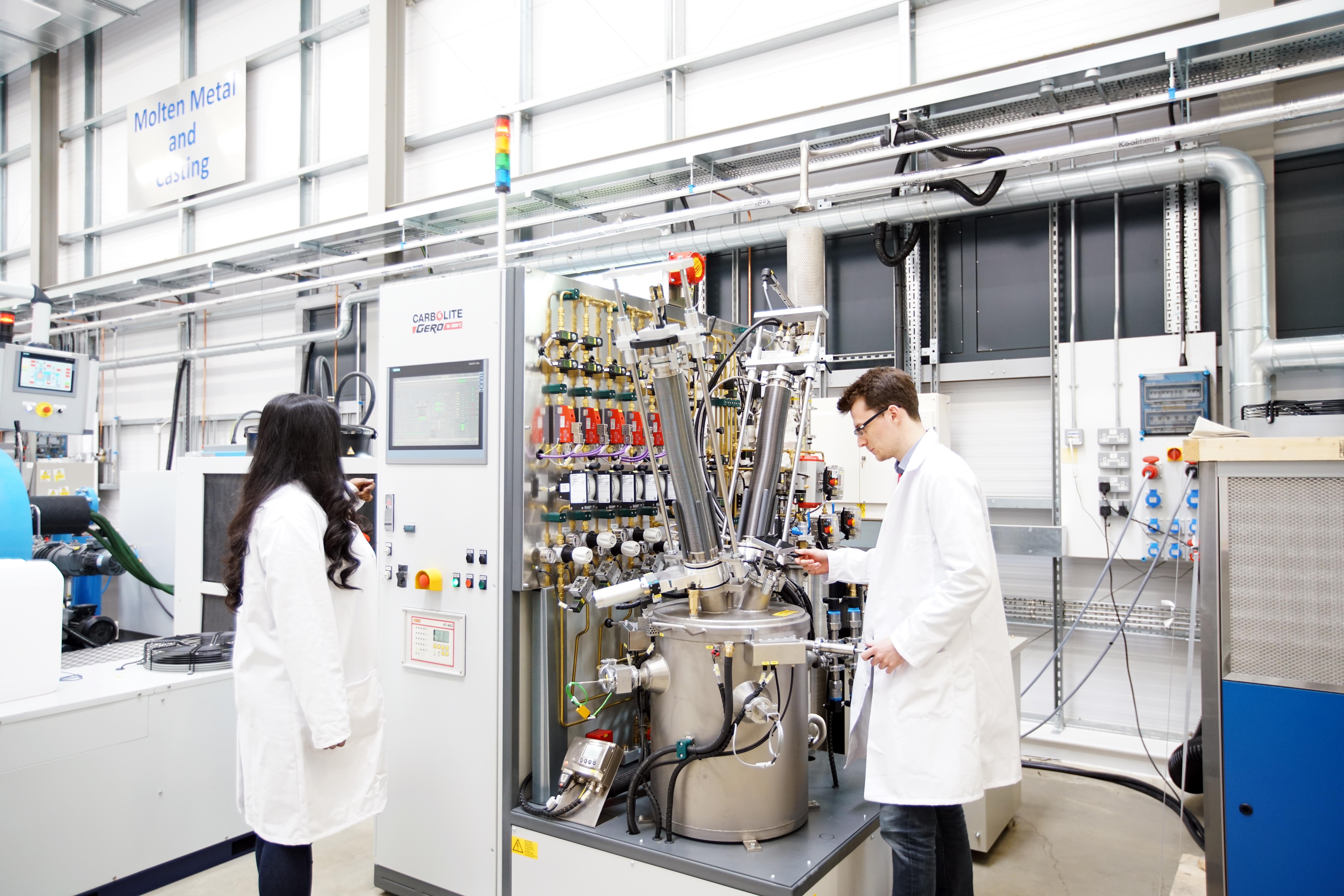
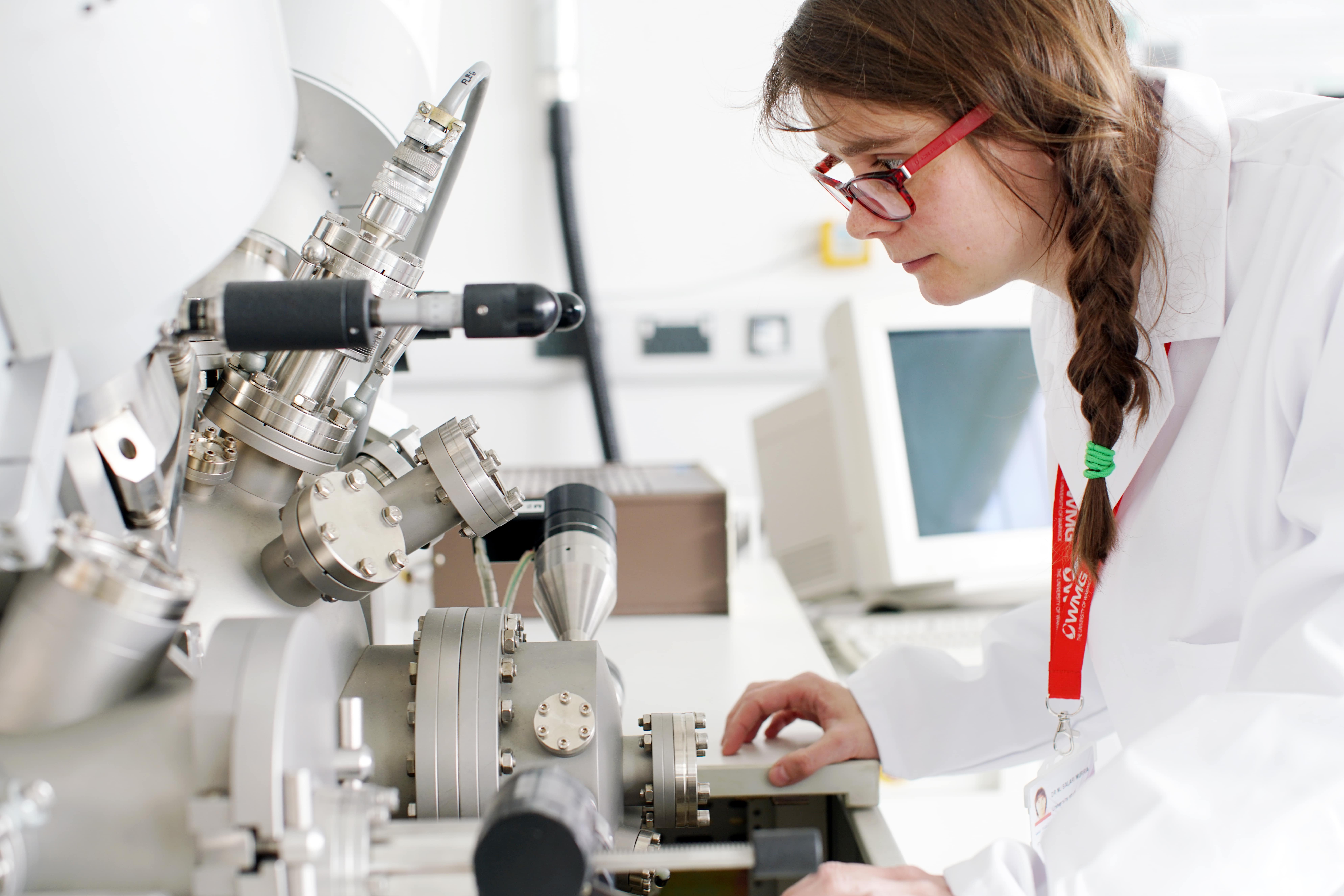
About our research
Microstructure properties research
We study the influence of microstructure on steel properties, led by Professor Claire Davis. Our focus includes understanding casting and reheating effects on microstructure, with a keen interest in microalloying element segregation and grain growth. Hot deformation processes like thermo-mechanical controlled rolling and forging are investigated for their impact on recrystallization and grain size development. In alloy steels, heat treatment and precipitation reactions post-hot deformation are crucial for final mechanical properties, with predictive models used.
Additionally, we develop non-contact, non-destructive evaluation techniques for steel microstructure using electromagnetic sensors. Collaborating with the University of Manchester, our work has led to the installation of these systems in steel mills, trialed for steel product characterization.
Steel coatings research
Our research extends to steel coatings, covering functional and industrial applications like galvanizing and electroplating. We focus on coatings such as aluminum, titanium, and nickel alloys. Investigating the microstructure, processing, and properties of alloys, we explore their behavior under challenging conditions, including extreme temperatures and loads. Studies encompass surface degradation processes like oxidation and their impact on microstructure, affecting overall steel performance.
Current research delves into alloy behavior in reducing and oxidizing environments, dwelling on fatigue and fretting. We employ isotopic tracers, SIMS, and electron microscopy to understand oxidation mechanisms, revealing insights into oxygen and hydrogen transport, the role of rare earth elements, and innovative analysis methodologies.
High temperature reactions
Understanding high-temperature reactions in steel processing requires in-situ observation, detailed characterization, and advanced modeling. We employ modern techniques such as confocal laser scanning microscopy, controlled atmosphere furnaces, O18 for oxidation tracking, droplet levitation furnace, high-temperature viscometer, mass spectrometer, and micro XCT to characterize and quantify these reactions. Additionally, we utilize state-of-the-art modeling tools like thermodynamic and phase field modeling to simulate high-temperature reactions and steel manufacturing processes.
Casting and thermo mechanical processing
The ability to produce bespoke steel compositions and process them to strip, as well as investigate solidification and hot deformation phenomenon is a key strength in the ASRC. The research includes examination of the effect of composition and cooling rate on microstructural development during solidification using instrumented moulds and hot deformation simulation with controlled temperature, strain and strain rate. This aids the development of both new casting methods such as twin roll or belt casting, as well as the development of new (or improvement of) alloys.
Electromagnetic (EM) sensors
Characterizing steel microstructures non-destructively, especially in-situ during processing, is desirable. Electromagnetic (EM) sensors, sensitive to magnetic and electrical properties influenced by microstructure, form the basis of our research.
We investigate the fundamental relationship between EM signals and microstructure using laboratory and commercial sensor systems, advanced magnetic domain imaging techniques, and multi-scale modeling.
Coatings and surface engineering
To ensure durability of engineered components coatings and surface modification are routinely applied. We work on development of new coatings and their inherent properties as well as understanding how both uncoated and coated materials perform in service, for example examining local corrosion behaviour and tribological behaviour.
Product and process characterisation
Characterization is crucial for understanding and modeling behavior. Our extensive facilities measure process parameters like viscosity and phase stability. Microscopy provides high-temperature texture information, compositional mapping, high-resolution imaging, and localized hardness tests. Modeling employs in-house code or commercial software.
Forming and joining
Warm or cold forming as well as joining are essential processes in the production of final component parts. We focus on examination of the role of the materials on processeability; for example local strain partitioning in dual phase steels using in-situ deformation in an SEM or formation of intermetallics in dissimilar weld joints using microscopy and tomography for 3D characterisation
Ready to work with WMG?
Register your interest in our steel research to start the conversation with us.